Heat treatment is a crucial process in the manufacturing industry that involves altering the properties of metals to enhance their strength, hardness, and durability. This process consists of three main stages: heating, soaking, and cooling. Each stage plays a vital role in achieving the desired metal properties. Let’s delve into these stages and understand their significance.
Heat Treatment Stages
The main heat treatment stages for steel and metals are:
- Heating,
- Soaking or holding.
- Cooling.
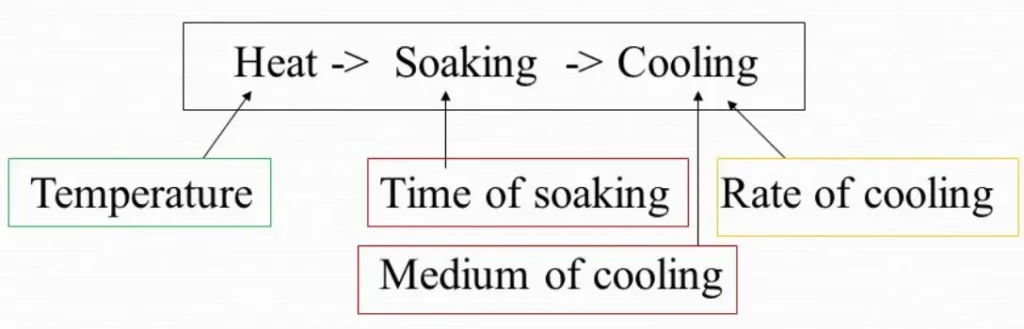
Stage 1: Heating the Metal
The initial stage of heat treatment involves slowly heating the metal to ensure a uniform temperature throughout. The primary objective here is to prevent distortion or cracking caused by uneven heating. By maintaining uniform temperatures, we can achieve consistent results.
The rate at which a metal is heated depends on various factors. One crucial factor is the heat conductivity of the metal itself. Metals with high heat conductivity heat up faster than those with low conductivity. Additionally, the condition of the metal also influences the heating rate. Hardened tools and parts require slower heating rates compared to untreated metals. Moreover, the size and cross-section of the metal play a role in determining the heating rate. Larger cross-sections necessitate slower heating to prevent warping or cracking.
Stage 2: Soaking the Metal
Once the metal reaches the desired temperature, it is held at that temperature for a specific duration. This stage is known as soaking. The purpose of soaking is to allow the internal structural changes to occur within the metal. The duration of soaking, known as the soaking period, depends on factors such as the chemical composition of the metal and the mass of the part being treated. In the case of steel parts with uneven cross-sections, the soaking period is determined by the largest section.
During the soaking stage, the metal is not immediately brought from room temperature to the final temperature. Instead, it is slowly preheated to a temperature just below the desired point of change. This preheating process ensures that the heat is evenly distributed throughout the metal. Once preheating is complete, the metal is quickly heated to the final required temperature.
In some cases, intricate parts may require multiple preheating steps to prevent cracking and excessive warping. For example, a complex part may need to be heated to 1500°F for hardening. In such instances, the part could be slowly heated to 600°F, soaked at that temperature, then gradually heated to 1200°F, and soaked again. Finally, the part would be rapidly heated to the hardening temperature of 1500°F.
It’s worth noting that nonferrous metals typically do not require preheating, as it can lead to an increase in grain size, which is undesirable for these metals.
Stage 3: Cooling the Metal
After the soaking stage, the metal must be cooled back to room temperature to complete the heat treatment process. The cooling stage is equally important as the previous stages and determines the final properties of the metal. The rate at which the metal is cooled depends on the desired properties and the type of metal being treated.
Quenching is a common cooling method that involves rapidly cooling the metal in a cooling medium such as oil, water, brine, or a combination of these. Quenching is often associated with hardening, as most metals are cooled rapidly during this process. However, it’s important to note that quenching doesn’t always result in increased hardness. For instance, copper is typically annealed by quenching it in water. Some metals, like air-hardened steels, require a relatively slow cooling rate for effective hardening.
Choosing the appropriate quenching medium is crucial, as different metals react differently to cooling. Metals that require rapid cooling rates are quenched in brine or water, while oil mixtures are more suitable for metals that need a slower cooling rate. Carbon steels are commonly water-hardened, while alloy steels are often oil-hardened. Non-ferrous metals, on the other hand, are typically quenched in water.
Conclusion
In conclusion, heat treatment is a multi-stage process that involves heating, soaking, and cooling the metal. Each stage contributes to achieving the desired properties, such as enhanced strength and hardness. By carefully controlling the temperature and cooling rate, manufacturers can optimize the properties of metals for various applications.