Steel is a versatile and widely used material in various industries, thanks to its exceptional strength and durability. However, steel in its raw form can be brittle and prone to cracking. To enhance its mechanical properties, steel undergoes a process called tempering.
In this article, you will learn what is steel tempering, how it works, purpose of tempering, methods, and the science behind its transformative effects.
What is Steel Tempering?
Tempering is a heat treatment process that involves reheating hardened steel to a specific temperature usually below AC3 line (723°C) and then cooling it gradually. This controlled heating and cooling process helps to reduce the hardness of the steel while improving its toughness and ductility. The goal of tempering is to strike a balance between hardness and flexibility, making the steel more suitable for its intended application.
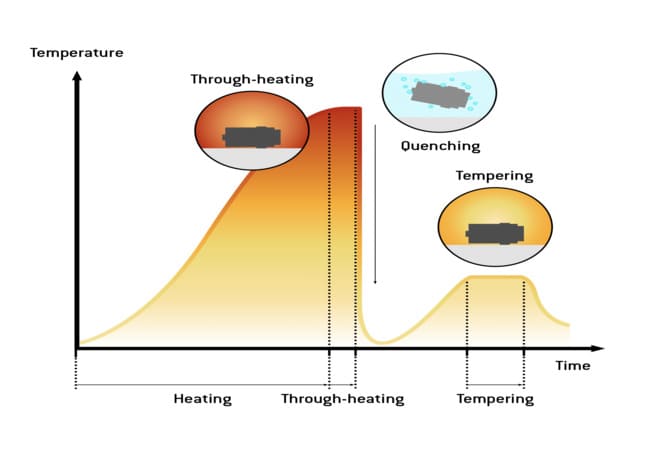
During tempering, the steel is heated below its critical temperature, which is the temperature at which the steel undergoes a phase change. The exact tempering temperature depends on the desired properties of the steel and the specific alloy composition. The steel is held at the tempering temperature for a certain period of time and then cooled slowly.
The Steel tempering stages are typically categorized as follows:
- Low-temperature tempering (80-200 °C): At this stage, the steel undergoes a process called “recovery,” where internal stresses are relieved, and some hardness is reduced. This stage helps improve the steel’s toughness and ductility.
- Medium-temperature tempering (200-350 °C): During this stage, the steel goes through a process called “recrystallization,” where new, more stable grains form. This further reduces hardness and increases toughness.
- High-temperature tempering (350-500 °C): In this stage, the steel undergoes “grain growth,” where the grains continue to grow, resulting in further reduction in hardness and increased toughness. This stage also helps relieve any remaining internal stresses.
- Very high-temperature tempering (500-550 °C): At this stage, the steel experiences “spheroidization,” where the carbides present in the steel transform into rounded particles. This process improves the steel’s machinability and reduces hardness.
In the first stage, the temperature is raised from 80 °C to around 200 °C. This stage is mainly for steels with a carbon content higher than 0.2%. During this stage, the ε carbides present in the martensite lattice are eliminated, and the distortion of the lattice decreases.
The second stage occurs at temperatures ranging from approximately 200 °C to 320 °C (higher in low-alloy steels). In this stage, any residual austenite present in the steel disintegrates, and carbides and α ferrite start to form.
Moving on to the third stage, the temperature is increased to around 320 °C to 520 °C. During this stage, a balance is achieved between ferrite and cementite, resulting in a substantial drop in hardness. At temperatures of 500 °C and higher, the cementite particles begin to coagulate to a greater extent.
Finally, in the fourth stage, the temperature is raised to approximately 450 °C to 550 °C. This stage is particularly relevant for higher alloy steels containing elements like chrome or tungsten. During this stage, special carbides formed by these alloy elements are eliminated, allowing for the achievement of greater hardness compared to martensite.
Here is a table showing the tempering temperature range for some common metals:
Metal | Tempering Temperature Range (°C) |
---|---|
Carbon Steel | 200-550 |
Stainless Steel | 300-600 |
Tool Steel | 500-700 |
Aluminum | 150-250 |
Copper | 250-400 |
Brass | 300-500 |
Bronze | 300-600 |
Please note that these temperature ranges are approximate and can vary depending on the specific alloy composition and desired properties. It’s always recommended to refer to the material’s technical specifications or consult with a metallurgical expert for precise tempering temperature guidelines.
Types of Tempering Heat Treatment
Types of tempering processes include:
- Differential tempering: This technique involves providing different amounts of temper to different parts of the steel. It is commonly used in bladesmithing to create knives and swords with a hard edge and a softer spine or center. By doing so, the toughness of the blade is increased while maintaining a sharp and impact-resistant edge. This method is more prevalent in Europe compared to the differential hardening techniques used in Asian swordsmithing.
- Interrupted quenching: This method, often referred to as tempering, is different from traditional tempering. It involves quenching the steel to a specific temperature above the martensite start temperature and holding it at that temperature for an extended period. Depending on the temperature and duration, this process allows the formation of pure bainite or delays the formation of martensite until internal stresses relax. Austempering and martempering are examples of interrupted quenching methods.
- Austempering: Austempering is a technique used to form pure bainite, which is a transitional microstructure between pearlite and martensite. The steel is quenched in a bath of molten metals or salts to rapidly cool it past the point where pearlite can form. It is then held at the bainite-forming temperature until the bainite fully forms. Austempering produces steel with superior impact resistance, greater strength, and toughness for a given hardness. It does not require further tempering.
- Martempering: Martempering is similar to austempering, but the goal is to create martensite instead of bainite. The steel is quenched to a lower temperature, just above the martensite start temperature, and held at that temperature until an equilibrium is reached. The steel is then removed from the bath before bainite can form and allowed to air-cool, transforming it into martensite. This process reduces the brittleness of the steel by allowing internal stresses to relax. However, martempered steel usually requires further tempering to adjust hardness and toughness, except in cases where maximum hardness is desired without compromising brittleness.
Tempering Colours Chart
The toughness-to-hardness ratio in steel varies depending on the temperature of the tempering process. The main objective of tempering is to precisely adjust this ratio. Furthermore, the surface color of the material changes due to oxidation. By observing the color of the treated steel, one can determine the tempering temperature and make inferences about its potential applications.
Tempering is commonly carried out within the temperature range of 160 °C to 600 °C. Temperatures below 300 °C and above 500 °C are known as low-temperature and high-temperature tempering, respectively. Additionally, tempering is divided into four stages based on temperature.
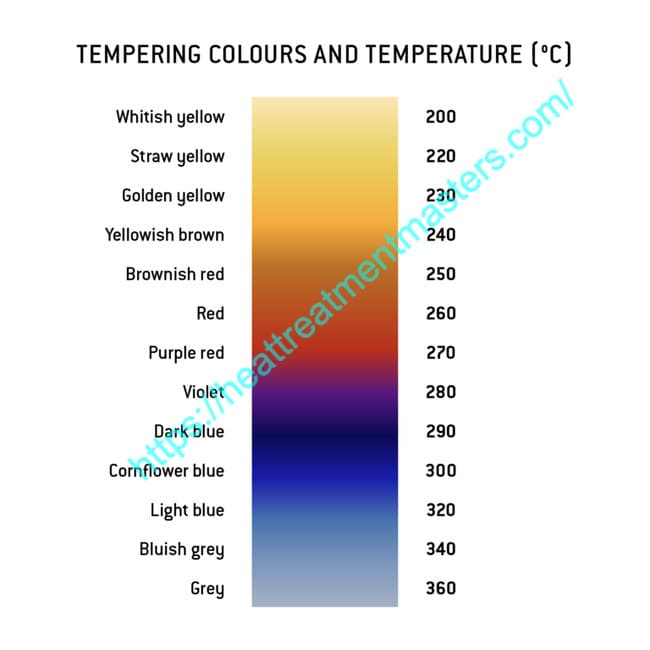
The Purpose of Tempering
The primary purpose of tempering is to relieve the internal stresses created during the initial hardening process. When steel is hardened, it becomes extremely hard but also brittle. This brittleness can lead to fractures and failures under certain conditions. Tempering helps to alleviate these issues by reducing the hardness and increasing the steel’s ability to absorb energy without breaking.
The main objectives of Tempering Heat Treatment Process are:
- Strengthening
- Reducing brittleness
- Improving toughness
- Enhancing ductility
- Increasing resistance to fatigue
- Minimizing residual stresses
- Controlling grain size and structure
- Improving machinability
- Enhancing corrosion resistance
- Achieving desired hardness levels
Tempering heat treatment cycle and stages
empering is a heat treatment process that is typically performed after a material has undergone a hardening process, such as quenching. The purpose of tempering is to reduce the hardness and brittleness of the material, while improving its toughness and ductility. The tempering process involves heating the material to a specific temperature and holding it at that temperature for a certain period of time, followed by cooling.
The tempering heat treatment cycle consists of several stages:
- Preheating: The material is heated slowly to a temperature below its critical point. This helps to ensure uniform heating and prevent thermal shock.
- Soaking: Once the preheating stage is complete, the material is held at the desired tempering temperature for a specific duration. This allows for the diffusion of carbon atoms within the material, which helps to relieve internal stresses and improve its mechanical properties.
- Cooling: After the soaking stage, the material is cooled down. The cooling rate can vary depending on the desired properties of the material. Slow cooling (air cooling) is often used for structural steels, while faster cooling methods like oil or water quenching may be employed for certain applications.
The Tempering Process:
- Preheating: The first step in tempering involves preheating the hardened steel to a specific temperature. This temperature is usually below the critical point, which is the temperature at which the steel undergoes a phase transformation.
- Holding: Once the steel reaches the desired temperature, it is held at that temperature for a specific duration. The duration depends on factors such as the steel’s composition, desired properties, and thickness.
- Cooling: After the holding period, the steel is slowly cooled down. The cooling rate is crucial, as rapid cooling can lead to the formation of undesirable microstructures and reduce the effectiveness of tempering.
How Tempering Heat Treatment works?
Here’s how the tempering process works:
- Preparing the material: The material, usually hardened steel, is first heated to a high temperature to achieve full hardness. This initial heat treatment is known as hardening or quenching.
- Heating to the tempering temperature: After the hardening process, the material is heated again, but this time to a lower temperature called the tempering temperature. The specific temperature depends on the desired mechanical properties and the type of steel being tempered.
- Holding at the tempering temperature: Once the material reaches the tempering temperature, it is held at that temperature for a specific period of time. This allows the internal structure of the material to adjust and relieve some of the internal stresses caused by the hardening process.
- Cooling: After the holding time, the material is cooled down either by air cooling or furnace cooling. The cooling rate during tempering is generally slower than during quenching. This controlled cooling helps to prevent the material from becoming too brittle.
The tempering process brings about several changes in the material’s properties. It reduces the hardness and brittleness caused by the hardening process, while simultaneously increasing toughness and ductility. The exact combination of properties achieved depends on the tempering temperature and time.
Effects of Tempering
During the tempering process, several changes occur within the steel’s microstructure. The most significant change is the transformation of retained austenite, a high-temperature phase, into a more stable structure called tempered martensite. This transformation reduces the hardness of the steel while increasing its toughness and ductility.
The exact properties achieved through tempering depend on the tempering temperature. Lower tempering temperatures result in higher hardness and strength, while higher temperatures yield lower hardness but increased toughness. The choice of tempering temperature is determined by the specific requirements of the steel’s application.
Applications of Tempered Steel
Tempered steel finds applications in a wide range of industries. Some common examples include:
- Automotive Industry: Tempered steel is used in the manufacturing of various automotive components, such as crankshafts, gears, and suspension systems. The tempered steel’s improved toughness and resistance to fatigue make it ideal for these demanding applications.
- Construction Industry: Tempered steel is utilized in the construction of buildings, bridges, and other infrastructure projects. Its enhanced strength and ductility ensure structural integrity and resistance to external forces.
- Tool and Die Making: Many cutting tools, such as drills, saw blades, and chisels, are made from tempered steel. The tempering process imparts the necessary hardness and toughness required for these tools to withstand the rigors of cutting and shaping operations.
Conclusion
Steel tempering is a vital heat treatment process that enhances the mechanical properties of steel, making it more suitable for a wide range of applications. By carefully controlling the tempering temperature and duration, manufacturers can achieve the desired balance between hardness, strength, and toughness. Understanding the science behind tempering allows engineers and designers to harness the full potential of steel, ensuring its optimal performance in various industries.