Vacuum heat treatment is a specialized thermal process that is conducted in a controlled vacuum environment. It involves heating a material or component to high temperatures and then subjecting it to various cooling and holding cycles. The absence of air or other gases in the vacuum chamber during the process offers several advantages compared to traditional heat treatment methods conducted in atmospheric conditions.
Understanding the Operational Principles of Vacuum Heat Treatment
Vacuum heat treatment is a technique employed to harden metals by subjecting them to extremely high temperatures. Unlike conventional methods, this process takes place within a vacuum chamber, where the pressure is significantly lower than atmospheric pressure, and the absence of air is ensured. This controlled vacuum environment plays a crucial role in creating an inert atmosphere, making it ideal for processing metal workpieces.
The presence of air during heat treatment can lead to undesired reactions with the metal, resulting in surfaces that are either harder or softer than intended. Vacuum heat treatment eliminates this concern by preventing oxidation and ensuring consistent and predictable outcomes.
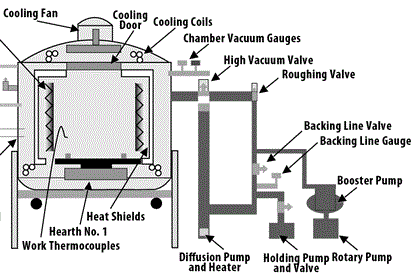
The process of vacuum heat treatment involves the utilization of a vacuum pumping system within the vacuum chamber to remove air and create a low-pressure environment. Once the air is evacuated, the metal workpiece is gradually heated to temperatures as high as 1,316 degrees Celsius, following a controlled heating rate. Subsequently, the temperature is carefully lowered according to the specific requirements of the part and its material. The duration of the soak time during this process is determined based on the desired outcomes and the characteristics of the workpiece.
Key aspects of vacuum heat treatment
- Vacuum Environment: The primary characteristic of vacuum heat treatment is the absence of air or any other reactive gases. This eliminates the risk of oxidation, decarburization, and contamination of the material being treated. It allows for precise control over the heat treatment process, ensuring consistent and predictable results.
- Heating: The material or component is heated in a vacuum furnace using electric heating elements or by induction heating. The absence of oxygen prevents surface reactions, such as scaling or discoloration, and helps maintain the material’s integrity.
- Cooling: Different cooling rates can be achieved during vacuum heat treatment by adjusting the cooling medium, such as gas or liquid quenching, or by controlled furnace cooling. The absence of gases allows for faster and more uniform cooling, reducing distortion and minimizing the formation of residual stresses.
- Heat Treatment Processes: Various heat treatment processes can be performed in a vacuum, including annealing, tempering, hardening, solutionizing, aging, and brazing. The specific process depends on the desired material properties and the application requirements.
Benefits of Vacuum Heat Treatment
Vacuum heat treatment involves heating materials in a vacuum chamber, where the absence of air or other reactive gases prevents oxidation and contamination. This controlled environment allows for precise temperature control and uniform heating, resulting in improved material properties.
- Enhanced Mechanical Properties: Vacuum heat treatment can significantly improve the mechanical properties of materials. By carefully controlling the heating and cooling rates, it is possible to achieve desirable characteristics such as increased hardness, improved wear resistance, and enhanced tensile strength.
- Reduced Distortion: One of the major advantages of vacuum heat treatment is the minimal distortion it causes to the material being treated. The absence of reactive gases eliminates the risk of surface reactions, resulting in a more uniform and controlled heat transfer. This ensures that the final product retains its original shape and dimensions, reducing the need for additional machining or finishing processes.
- Clean and Contamination-Free: The vacuum environment eliminates the presence of oxygen and other impurities, preventing oxidation and contamination of the material. This is particularly beneficial for materials that are highly sensitive to oxidation, such as certain alloys and steels. The clean and contamination-free nature of vacuum heat treatment ensures the integrity and purity of the treated material.
Advantages of Vacuum heat treatment
The main advantages of Vacuum heat treatment are:
- No decarburization
- No oxidation of components – bright surfaces
- High temperature uniformity – low distortion
- Defined temperature guidance by load thermocouples – reproducible results
- Documentation of load regarding the time/temperature cycle and actual values
- Full automation of heat treatment process
Applications of Vacuum Heat Treatment
- Aerospace Industry: Vacuum heat treatment finds extensive use in the aerospace industry, where the demand for high-performance materials is paramount. Components such as turbine blades, landing gear, and structural parts undergo vacuum heat treatment to enhance their strength, fatigue resistance, and overall performance.
- Automotive Industry: Vacuum heat treatment plays a vital role in the automotive industry, where components like gears, shafts, and springs require improved mechanical properties. Vacuum carburizing, a specific type of vacuum heat treatment, is widely used to enhance the wear resistance and durability of these components.
- Tool and Die Industry: Vacuum heat treatment is instrumental in the tool and die industry, where the performance and longevity of cutting tools, molds, and dies are critical. By subjecting these components to vacuum heat treatment, their hardness, toughness, and resistance to wear can be significantly improved, resulting in longer tool life and reduced downtime.
The Future of Vacuum Heat Treatment
As technology continues to advance, the future of vacuum heat treatment looks promising. Researchers are exploring new techniques and processes to further enhance the capabilities of this method. The integration of advanced computer simulations, automation, and data analytics will enable more precise control over the heat treatment process, leading to even better material performance.
Furthermore, the development of novel materials, such as advanced alloys and composites, will require tailored heat treatment processes. Vacuum heat treatment is expected to play a crucial role in unlocking the full potential of these materials, enabling engineers to push the boundaries of performance and efficiency.
Limitations of Vacuum Heat Treatment
While vacuum heat treatment offers numerous advantages, it also has some limitations. Here are a few limitations associated with vacuum heat treatment:
- Cost: Vacuum heat treatment equipment is typically more expensive to purchase, operate, and maintain compared to traditional heat treatment methods conducted in atmospheric conditions. The need for a vacuum chamber, specialized heating elements, and vacuum pumps adds to the overall cost.
- Size Limitations: Vacuum heat treatment chambers have size limitations, and the size of the components that can be processed is restricted by the available chamber dimensions. Large or bulky components may be challenging to accommodate within the vacuum furnace, requiring alternative heat treatment methods.
- Limited Heat Transfer: The absence of a gaseous medium in a vacuum environment hinders heat transfer by convection. As a result, heat transfer occurs primarily through radiation and conduction, which can be slower compared to convective heat transfer. This limitation can affect the heat treatment process, especially for parts with complex geometries or sections that require rapid and uniform heating or cooling.
- Longer Processing Time: Due to the slower heat transfer in a vacuum environment, heat treatment cycles may take longer compared to traditional methods. Achieving the desired material properties and heat treatment results may require extended processing times, which can impact production schedules and lead to increased costs.
- Limited Process Flexibility: Some heat treatment processes, such as certain types of surface treatments or reactions that require specific gas atmospheres, cannot be performed in a vacuum environment. The absence of reactive gases restricts the range of processes that can be carried out, limiting the versatility of vacuum heat treatment.
- Vacuum Integrity: Maintaining the integrity of the vacuum chamber is crucial for the success of vacuum heat treatment. Any leakage of air or contaminants into the chamber can compromise the quality and consistency of the heat treatment process. Regular maintenance and monitoring of the vacuum system are necessary to ensure proper functioning and prevent potential issues.
Despite these limitations, vacuum heat treatment remains a valuable and widely used method for achieving precise and controlled heat treatment of materials, particularly for applications that require high-purity, clean, and distortion-free results.