Heat treatment is a widely used technique in metallurgy to modify the properties of metals, and one of the intriguing phenomena observed during this process is the increase in hardness.
Understanding why metals become harder when heat treated requires delving into the metallurgical changes that occur. In this blog post, we will explore the underlying mechanisms and provide practical examples to illustrate the concept.
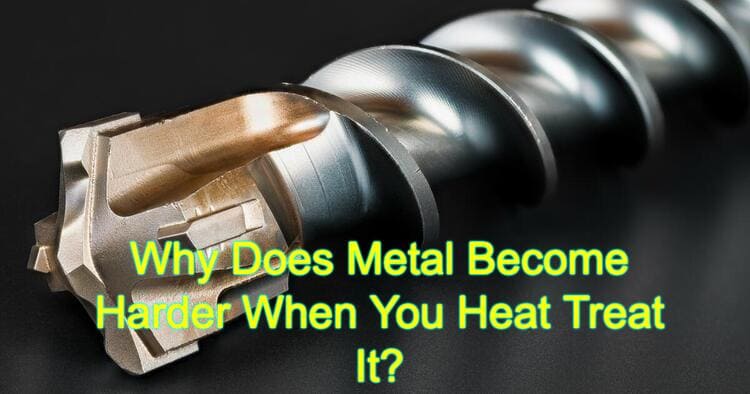
Metallurgical Changes
When a metal is heated and subsequently cooled, its internal structure undergoes transformations that contribute to the increase in hardness.
Two primary processes occur during heat treatment:
- Phase transformations and
- Grain structure modifications.
Phase Transformations
Heat treatment involves heating the metal to specific temperatures, leading to phase changes within its microstructure. For example:
- Austenite Formation: In steels, heating above the critical temperature results in the formation of austenite, a high-temperature phase with a face-centered cubic (FCC) crystal structure.
- Martensitic Transformation-Rapid cooling, or quenching, from the austenitic phase converts it into martensite, a hard and brittle phase with a body-centered tetragonal (BCT) crystal structure. This transformation contributes to increased hardness.
Grain Structure Modifications
Heat treatment also influences the grain structure of the metal, which affects its mechanical properties.
- Grain Refinement– Annealing, a heat treatment process involving slow cooling, promotes the growth of larger grains. This can enhance the metal’s ductility but reduces its hardness.
- Grain Size Reduction– Quenching from high temperatures, as in the case of martensitic transformation, can result in a fine-grained microstructure. The smaller grain size contributes to increased hardness.
- Grain Size Increase– Normalizing on other hand increases the grain size.
Practical Examples
Let’s consider some practical examples to illustrate the concept of increased hardness through heat treatment:
- Knife Blades: High-carbon steel blades used in knives undergo heat treatment to achieve the desired hardness. After heating the steel to austenitizing temperature, rapid quenching transforms it into martensite, making the blade hard and capable of retaining a sharp edge.
- Automotive Components: Various automotive components, such as crankshafts or gears, undergo heat treatment for improved strength and wear resistance. Controlled heating and cooling processes modify the metal’s internal structure, resulting in a hardened surface layer while maintaining a tough core.
- Tool Steels: Tools like drill bits, punches, or dies often require high hardness to withstand the demanding conditions of machining or forming operations. Heat treatment, including quenching and tempering, allows the steel to achieve the desired hardness level, ensuring prolonged tool life.