1018 Steel
The Versatile Low-Carbon OptionOne widely used steel grade is 1018, known for its versatility and affordability. Classified as a mild steel, it finds its application in various everyday uses.
Some common examples include mounting plates, pump parts, motor shafts, tie rods, pins, and bushings. With its low carbon content (less than 0.30%), 1018 steel offers excellent machinability and weldability. Additionally, due to its relatively soft nature, it can be easily swaged, crimped, and bent.
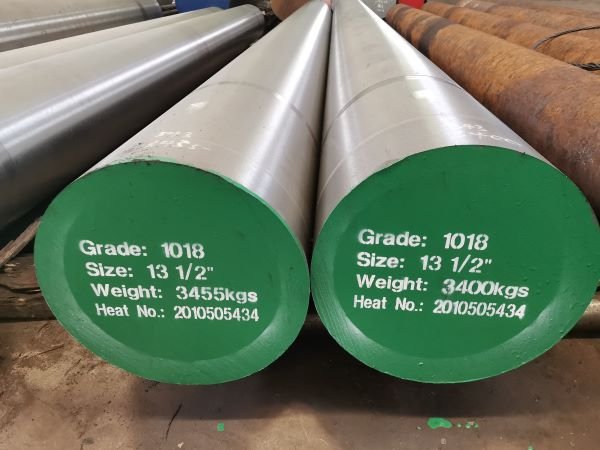
Compared to other steel grades, 1018 is considered one of the least expensive options. However, its hardenability is limited to case hardening or carburizing, a process that creates a hard exterior while maintaining a relatively soft core. This characteristic sets it apart from 4140 steel.
4140 Steel: High-Tensile Chrome-Molybdenum Strength
In contrast to 1018 steel, 4140 steel possesses higher carbon content, indicated by the last two digits (0.40%). Beyond carbon, it incorporates small amounts of chromium and molybdenum, elements that significantly enhance its metallurgical properties. These additions contribute to increased strength, hardness, and corrosion resistance.
The ultimate tensile strength of 4140 steel is approximately 50% higher than that of 1018 steel, making it an excellent choice for parts requiring superior impact resistance and torsional strength. It finds applications in connecting rods, crankshafts, machine tools, jigs, molds, fixtures, as well as the logging industry and oil and gas applications.
While 4140 steel exhibits machinability, it is not as readily weldable or formable as 1018 steel. Proper post-welding heat treatment is necessary to prevent brittleness.
1018 vs. 4140 Steel chemical compositions
When comparing the chemical compositions of 1018 and 4140 steel, there are notable distinctions.
1018 Steel typically contains approximately 0.15-0.20% carbon (C), 0.60-0.90% manganese (Mn), and small amounts of phosphorus (P), sulfur (S), and silicon (Si). It does not contain significant amounts of chromium (Cr) or molybdenum (Mo).
On the other hand, 4140 Steel consists of approximately 0.38-0.43% carbon (C), 0.75-1.00% manganese (Mn), and low levels of phosphorus (P) and sulfur (S). Additionally, it contains 0.15-0.35% silicon (Si), 0.80-1.10% chromium (Cr), and 0.15-0.25% molybdenum (Mo).
Chemical Composition | 1018 | 4140 |
---|---|---|
Carbon (C) | 0.15-0.20% | 0.38-0.43% |
Manganese (Mn) | 0.60-0.90% | 0.75-1.00% |
Phosphorus (P) | 0.04% max | 0.035% max |
Sulfur (S) | 0.05% max | 0.04% max |
Silicon (Si) | 0.15-0.35% | 0.15-0.35% |
Chromium (Cr) | – | 0.80-1.10% |
Molybdenum (Mo) | – | 0.15-0.25% |
1018 vs. 4140 Steel Mechanical Properties
When comparing the mechanical properties of 1018 and 4140 steel, notable differences emerge. In terms of tensile strength, 4140 steel outperforms 1018 steel with a value of 655 MPa (95,000 psi) compared to 370 MPa (54,000 psi) for 1018 steel.
Similarly, 4140 steel exhibits a higher yield strength of 415 MPa (60,000 psi) compared to 330 MPa (48,000 psi) for 1018 steel. Elongation, which measures the ability of a material to deform before fracturing, is higher for 4140 steel at 25% compared to 15% for 1018 steel.
Property | 1018 Steel | 4140 Steel |
---|---|---|
Tensile Strength | 370 MPa (54,000 psi) | 655 MPa (95,000 psi) |
Yield Strength | 330 MPa (48,000 psi) | 415 MPa (60,000 psi) |
Elongation | 15% | 25% |
Hardness | Brinell: 126 | Brinell: 197 |
Rockwell B: 71 | Rockwell C: 22 | |
Young’s Modulus (E) | 200 GPa (29,000 ksi) | 205 GPa (29,700 ksi) |
Density | 7.87 g/cm³ (0.284 lb/in³) | 7.85 g/cm³ (0.283 lb/in³) |
Melting Point | Approximately 1480°C | Approximately 1460°C |
Thermal Conductivity | 49.8 W/m·K (346 BTU/hr·ft·°F) | 42.7 W/m·K (296 BTU/hr·ft·°F) |
Specific Heat Capacity | 0.49 J/g·K (0.12 BTU/lb·°F) | 0.46 J/g·K (0.11 BTU/lb·°F) |
Electrical Conductivity | 15-20% IACS | 10-15% IACS |
Hardness measurements also differ, with 4140 steel having a Brinell hardness of 197 and Rockwell C hardness of 22, while 1018 steel has a Brinell hardness of 126 and Rockwell B hardness of 71.
These variations in mechanical properties make 4140 steel a preferred choice for applications requiring higher strength and hardness, while 1018 steel offers more flexibility in terms of machinability and formability.
Comparing the Two: Factors to Consider
When choosing between 1018 and 4140 steel, several factors come into play. Both steel grades have their advantages and considerations:
- Machinability: 1018 steel offers excellent machinability, while 4140 steel requires lower cutting speeds and feedrates due to its higher hardness.
- Hardness and Strength: 4140 steel surpasses 1018 steel in terms of ultimate tensile strength, hardness, and fatigue strength.
- Weldability: 1018 steel is more weldable than 4140 steel, which requires specific procedures and heat treatment to maintain its properties.
- Corrosion and Wear Resistance: Thanks to its higher carbon content and alloying elements, 4140 steel exhibits superior resistance to corrosion, heat, and wear.
Applications:
1018 Steel is commonly used in a variety of general-purpose applications, such as shafts, pins, studs, bolts, and machinery parts. It is suitable for applications that do not require high strength or specialized properties.
On the other hand, 4140 Steel is often chosen for applications that demand higher strength and toughness, such as automotive components, gears, crankshafts, and tooling. Its superior mechanical properties make it well-suited for heavy-duty and high-stress applications.
Machining:
1018 Steel is known for its excellent machinability, thanks to its lower carbon content and softer composition. It can be easily machined into various shapes and forms, making it ideal for machining operations such as drilling, turning, and milling.
While 4140 Steel is more challenging to machine due to its higher carbon content and higher hardness, it can still be machined with suitable cutting tools and machining techniques. However, it may require slower cutting speeds and more robust machinery.
Heat Treatment:
Both 1018 and 4140 Steel are amenable to heat treatment processes to enhance their properties. 1018 Steel is typically not heat treated as it already possesses good machinability and strength in its as-rolled condition.
In contrast, 4140 Steel is often subjected to heat treatment to achieve desired mechanical properties. Heat treatment methods such as quenching and tempering can increase its hardness, strength, and toughness, making it suitable for demanding applications.
Weldability:
1018 Steel exhibits good weldability and can be easily welded using common welding techniques, such as arc welding and spot welding. It does not require preheating or post-weld heat treatment in most cases.
On the other hand, 4140 Steel has lower weldability due to its higher carbon content and alloying elements. Preheating and post-weld heat treatment are often necessary to minimize the risk of cracking and achieve satisfactory weld quality.
Corrosion Resistance:
In terms of corrosion resistance, neither 1018 nor 4140 Steel are particularly corrosion-resistant. They are both considered to have fair to poor corrosion resistance, especially in corrosive environments such as marine or acidic conditions.
To improve corrosion resistance, additional protective measures such as coatings, plating, or the use of corrosion-resistant alloys may be required.
Strength:
4140 Steel offers significantly higher strength compared to 1018 Steel. Its higher carbon content and alloying elements contribute to its superior strength properties, making it suitable for applications requiring high strength and durability. In contrast, 1018 Steel has lower strength but provides sufficient strength for general-purpose applications where high strength is not a primary requirement.
Cost:
In terms of cost, 1018 Steel is generally more affordable compared to 4140 Steel. The lower alloy content and simpler composition of 1018 Steel contribute to its lower cost. On the other hand, 4140 Steel, being an alloy steel with additional alloying elements, tends to be relatively more expensive.