Spring steel is a versatile and widely used material known for its exceptional strength and resilience. It finds applications in various industries, including automotive, aerospace, manufacturing, and construction. One of the key factors that contribute to its remarkable properties is the heat treatment process.
In this article, we will delve into the world of spring steel heat treatment, exploring its significance, methods, and the resulting benefits.
Understanding Spring Steel
Before we dive into the heat treatment process, it’s essential to understand the characteristics of spring steel.
Spring steel is a low-alloy, medium-to-high carbon steel that exhibits excellent elasticity and fatigue resistance. It is specifically designed to withstand repeated bending or twisting without permanent deformation. The heat treatment process further enhances these properties, making it an ideal choice for springs, suspension systems, and other applications requiring high strength and durability.
To ensure optimal performance in springs with unique qualities like excellent fatigue resistance, non-magnetic properties, resistance to corrosion, high temperature tolerance, and minimal deformation, specific factors need to be taken into account.
The maximum safe stress for springs is determined by two key factors:
- the elastic limit or proportional limit in tension, and
- the torsional proportional limit.
Exceeding these stress values would cause permanent deformation, preventing the spring from returning to its initial state.
Classification of Spring Materials Based on Stiffness
The stiffness of spring materials can be categorized into three classes:
- (i) Nickel and steels (carbon and alloy) possess a tension modulus of 200 GNm-2.
- (ii) Bronze and other copper alloys have a modulus of 103.5 GNm-2.
- (iii) Monel metal, aluminium bronze, and beryllium copper have a modulus that falls between that of steel and bronze.
Importance of Stiffness in Spring Materials
Stiffness, which refers to the ability to resist sagging and distortion under load, is a crucial property of spring materials. Springs made from high modulus materials exhibit small load deflections, while those made from low modulus materials experience larger deflections.
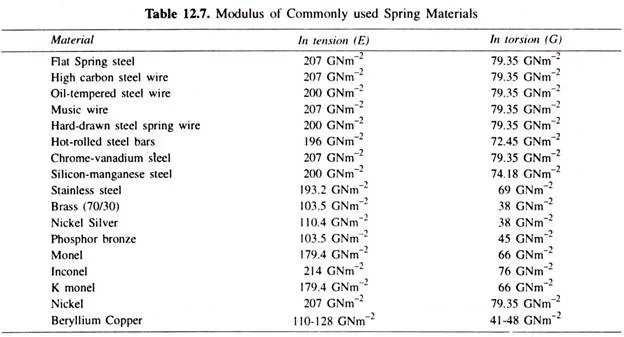
Significance of Heat Treatment for Spring Steel
Heat treatment is a controlled process that alters the microstructure of steel to achieve desired mechanical properties. In the case of spring steel, the primary objectives of heat treatment are to increase its hardness, improve its elastic limit, and enhance its resistance to fatigue and stress relaxation. By carefully manipulating the heating and cooling cycles, manufacturers can tailor the material’s properties to meet specific application requirements.
Spring Steel Heat Treatment Methods
- Annealing: The first step in spring steel heat treatment is annealing. This involves heating the steel to a specific temperature and holding it there for a predetermined time, followed by controlled cooling. Annealing relieves internal stresses, refines the grain structure, and improves machinability.
- Quenching: Quenching is a rapid cooling process that involves immersing the heated steel into a quenching medium, such as oil or water. This sudden cooling transforms the steel’s microstructure, increasing its hardness and strength. The choice of quenching medium depends on the desired properties and the steel’s composition.
- Tempering: After quenching, the steel is often too brittle and prone to cracking. Tempering is a process that involves reheating the steel to a specific temperature and holding it there for a specific time, followed by controlled cooling. This step reduces the brittleness and improves the toughness and ductility of the steel, making it less prone to fractures.
Heat Treatment temperature for Spring Steel
- Watch springs, which are only a few tenths of a millimeter thick, undergo tempering at temperatures ranging from 160 to 300°C after being quenched.
- Leaf springs with thicknesses of 1-3 mm are tempered at temperatures between 300 and 400°C. This tempering process is recommended for small helical and torsion springs.
- Music wire, after being coiled, undergoes low-temperature heat treatment at temperatures ranging from 260 to 290°C. This treatment helps relieve stresses within the wire caused by cold work during coiling. It also increases the elastic limit of the wire in the spring and its resistance to deformation during use.
- Hot forming of springs is carried out at temperatures between 920 and 830°C.
- Annealing of springs is done at temperatures ranging from 640 to 680°C.
- The main heat treatment process involves slow heating to temperatures between 830 and 860°C in a neutral atmosphere, followed by oil quenching to achieve a hardness of 42-48 HRC. The springs are then tempered at temperatures ranging from 430 to 500°C.
- Cutlery-type hardenable steel is initially formed into springs in an annealed state. It is then hardened at temperatures of 1000-1010°C and tempered at 315°C. However, tempering between 315 and 480°C can make the steel brittle.
Benefits of Spring Steel Heat Treatment:
- Increased Strength: Heat treatment significantly enhances the strength and hardness of spring steel, allowing it to withstand high stresses and loads without permanent deformation.
- Improved Fatigue Resistance: By manipulating the microstructure, heat treatment improves the material’s resistance to fatigue, enabling it to endure repeated cycles of loading and unloading without failure.
- Enhanced Elasticity: Heat-treated spring steel exhibits excellent elasticity, allowing it to return to its original shape after being subjected to bending or twisting forces.
- Reduced Stress Relaxation: Heat treatment minimizes stress relaxation, ensuring that the spring maintains its load-carrying capacity over an extended period.